WORKSHOPS
CREATE. LEARN. SHARE
Atelier Quinze offers a number of workshops and one-to-one classes. With a large, fully-equipped, ground floor workshop, individual work benches on the first floor, and the weaving and textiles studio on the second floor, we are well equipped for lots of activities. See below for the current timetable of workshops. If you join my newsletter I will let you know when new workshops are added.
​
As well as individual workshops we are planning to organise social get togethers where we meet up to make things (if we want), chat over a cup of tea or coffee and generally chill and meet like-minded folk for a couple of hours.
CREATE. LEARN. SHARE
Atelier Quinze offers a number of workshops and one-to-one classes. With a large, fully-equipped, ground floor workshop, individual work benches on the first floor, and the weaving and textiles studio on the second floor, we are well equipped for lots of activities. See below for the current timetable of workshops. If you join my newsletter I will let you know when new workshops are added.
​
As well as individual workshops we are planning to organise social get togethers where we meet up to make things (if we want), chat over a cup of tea or coffee and generally chill and meet like-minded folk for a couple of hours.
CREATE. LEARN. SHARE
Atelier Quinze offers a number of workshops and one-to-one classes. With a large, fully-equipped, ground floor workshop, individual work benches on the first floor, and the weaving and textiles studio on the second floor, we are well equipped for lots of activities. See below for the current timetable of workshops. If you join my newsletter I will let you know when new workshops are added.
​
As well as individual workshops we are planning to organise social get togethers where we meet up to make things (if we want), chat over a cup of tea or coffee and generally chill and meet like-minded folk for a couple of hours.
WORKSHOPS
CREATE. LEARN. SHARE
Atelier Quinze offers a number of workshops and one-to-one classes. With a large, fully-equipped, ground floor workshop, individual work benches on the first floor, and the weaving and textiles studio on the second floor, we are well equipped for lots of activities. See below for the current timetable of workshops. If you join my newsletter I will let you know when new workshops are added.
​
As well as individual workshops we are planning to organise social get togethers where we meet up to make things (if we want), chat over a cup of tea or coffee and generally chill and meet like-minded folk for a couple of hours.

How they're made...
Ever wondered how glass beads are made? Well here is the answer.
Lampwork glass beads are made by melting rods of glass in a torch flame. Nowadays a gas/oxygen mix torch is used but in the past beadmakers would use oil lamps - hence the name. The glass we use comes in a huge range of colours and types so the effects can literally be unlimited. Normally beadmakers use what is called soft glass but also a harder glass called borosilicate is available, which quite often is used by glass marble makers and flame workers. The two types are not compatible so cannot be used together in one bead.

The process of making beads can be quite involved. Whilst a simple, plain coloured bead may only take a few moments to make, decorative, larger beads can take much longer. Typically a set of larger beads will take me 3 or 4 hours to make plus annealing time. For me that is where the interest lies.
I have always been attracted to beads I can't buy elsewhere (and why I took up lampworking in the first place) and that are a challenge to make. I want to push that glass to do interesting things with colour, texture and shape. It really can be like alchemy and you cannot ever be sure just what will come out of the kiln the next day.
A beautifully shaped, well-made bead is a joy to behold and when you have seen one it makes you appreciate the difference between art and mass-produced lampwork beads.
The bead is made when glass is melted and wrapped around a metal mandrel (the mandrel forms the hole in the bead) before being decorated with various techniques such as twisted cane, metal leaf, millefiori, wire or dichroic glass. The beads are then shaped - by hand or with brass or graphite presses and tools - before being annealed in a kiln. Annealing removes the stresses created during the making process and lampwork beads should always be annealed to ensure longevity and it is a sign of quality. If you've ever purchased mass-produced, cheap, glass beads and found they have cracked with use, chances are they weren't annealed in a kiln.

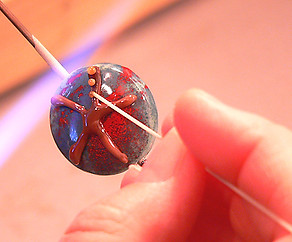



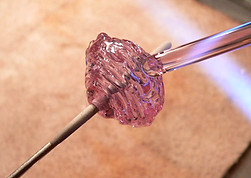
After annealing, the beads are manually cleaned to remove all traces of the bead release (put on the mandrel to stop the glass from sticking to the metal). Cheap beads often do not undergo this process because it can cause cracking in non-annealed beads so if you have ever wondered what that powdery residue inside bead holes is, now you know!
​
If you would like to see the bead making process you are welcome to visit my studio in La Trimouille for a demo. Drop me a line and we'll arrange a visit.
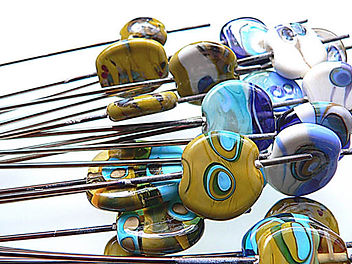